Panoval Label S.A. se fundó originalmente en 1991, en Suiza. Aprovechando las fortalezas de la compañía en el Lejano Oriente, Panoval (Asia) se estableció en la ciudad de Ho Chi Minh, Vietnam, en 2017. Esta instalación de última generación construida específicamente incluye múltiples líneas de recubrimiento y una instalación certificada ISO Clase 6. Sala blanca para productos de alta gama que requieren lo último en tecnología de recubrimiento. La empresa también está certificada según ISO 14644-2.
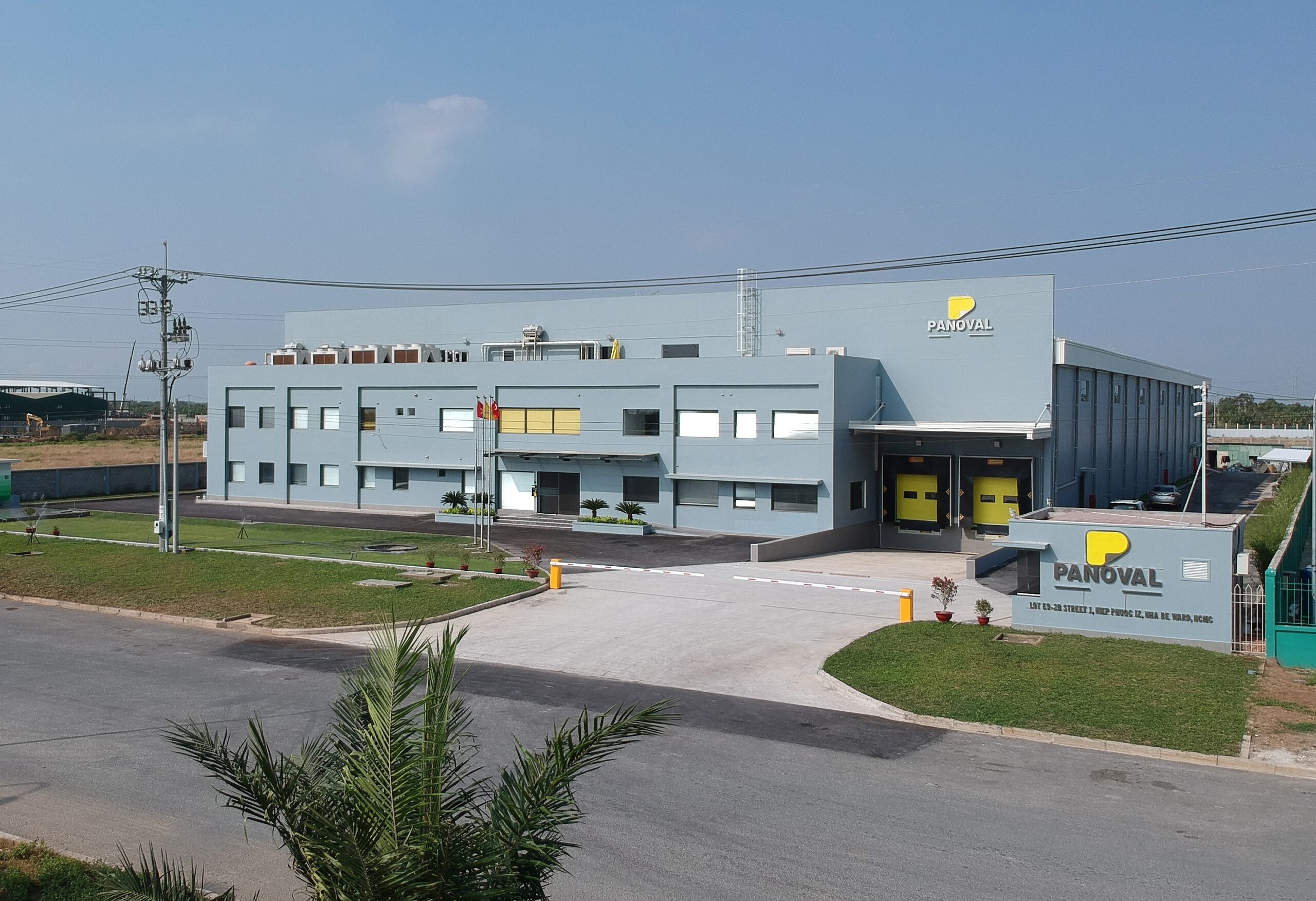
Más del 60% del volumen mundial de etiquetas adhesivas sensibles a la presión se producen en el Lejano Oriente, incluidas aquellas para aplicaciones electrónicas, médicas y farmacéuticas. Esta es la razón principal por la que la empresa se fundó en Vietnam, aunque la propiedad general sigue siendo europea. A pesar de tener un solo sitio de producción, Panoval trabaja internacionalmente con revendedores y clientes directos, y ha construido un negocio con presencia global. Su agilidad de producción y su reputación de flexibilidad los ha llevado a convertirse en un proveedor líder de etiquetas especializadas y no estándar. Los clientes típicos son revendedores de envases flexibles, convertidores de etiquetas e impresores convencionales.
Panoval emplea actualmente a 25 personas y está en constante expansión. El equipo directivo está formado por profesionales experimentados y operativos a nivel internacional con amplia experiencia en el desarrollo y producción de laminados de etiquetas para las aplicaciones más exigentes. El director Wilco van Zwieten se incorporó a Panoval como director de ventas en 1993 y ahora es una parte clave de ese equipo. Su cometido es impulsar nuevos negocios y considera que el avance tecnológico y la innovación son fundamentales para su éxito. Como él mismo explica: “En un mercado tan competitivo, es el tamaño relativamente pequeño de la empresa y el funcionamiento de dos líneas de recubrimiento muy diferentes lo que nos permite tener tanto éxito. Además del trabajo general de mayor volumen que realizamos, nuestro equipo de producción puede realizar una multitud de trabajos especializados más pequeños, a veces cambiando el producto tres o cuatro veces en un turno. Utilizamos la última tecnología de fusión en caliente UV para respaldar nuestros sistemas a base de caucho. Esta tecnología UV es la única que potencialmente puede reemplazar los recubrimientos a base de solventes… no de inmediato, sino dentro de diez a quince años. Para hacer esto, necesita tener una solución de curado UV de alta gama con todas las comodidades que respalden esa tecnología. Y eso es lo que diseñamos, en colaboración con los fabricantes de máquinas y GEW, para poder satisfacer todas nuestras necesidades en los próximos cinco a diez años. Estamos preparados para el futuro”.
Diseñado y fabricado en el Reino Unido por GEW, el sistema de curado UV personalizado de Panoval incluye cinco cabezales de lámpara NUVA2, con capacidad para albergar hasta siete cabezales en total, montados contra un rodillo enfriado de Ø1000 mm en una línea de recubrimiento de Sung An Machinery (SAM). Las lámparas están montadas alrededor del tambor en un conjunto de marco sólido, que está separado del conjunto de rodillos y se desliza fuera de su posición acoplada sobre rieles. Esto permite el acceso a la superficie del rodillo y a la parte inferior del conjunto del cabezal de la lámpara.
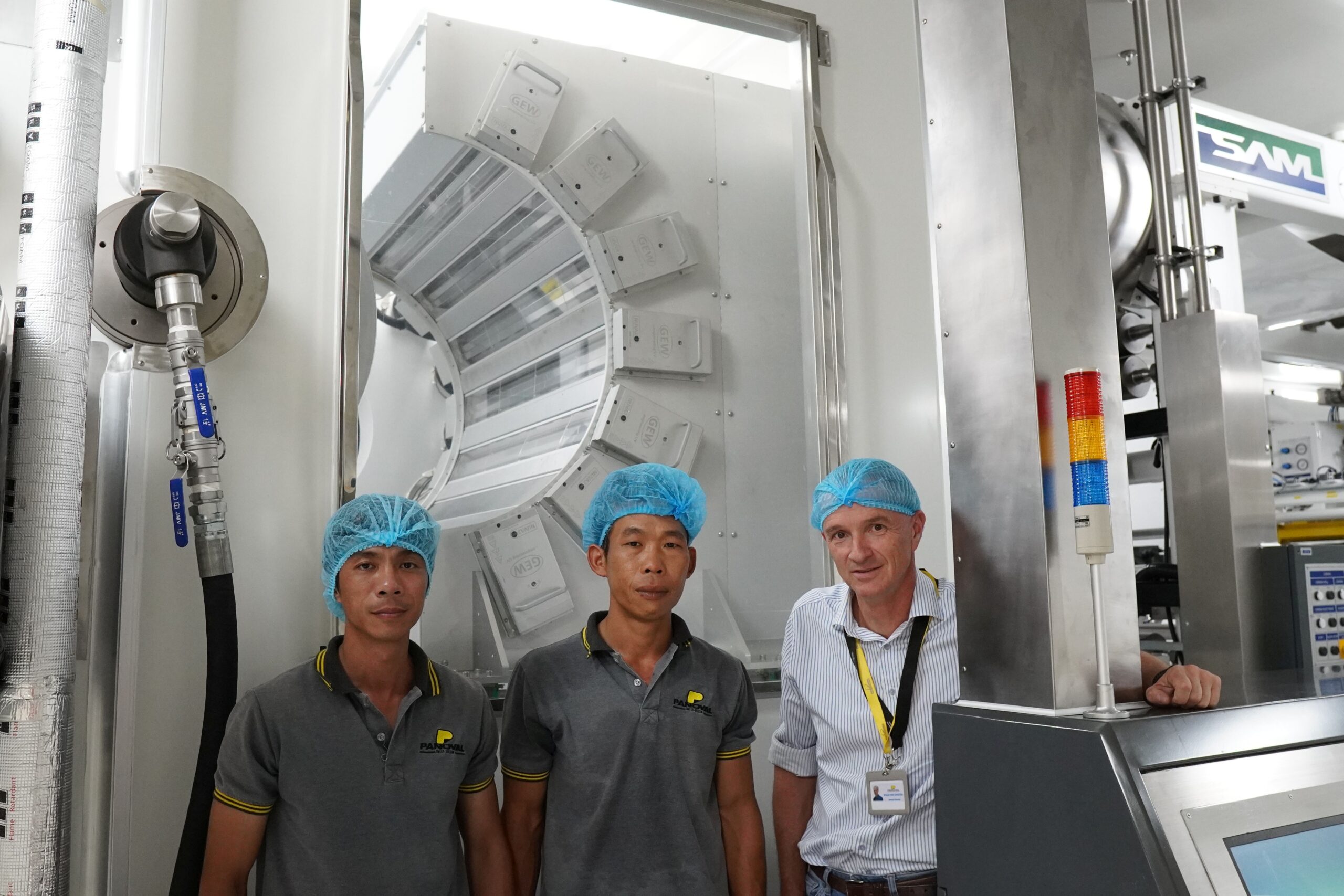
Cuando van Zwieten buscaba inicialmente una solución de curado UV, un asociado malasio que había trabajado recientemente con GEW para el diseño y la instalación de un sistema de curado UV para aplicaciones de recubrimientos antiadherentes se dirigió a GEW. Van Zwieten recuerda: “Visité la fábrica de Malasia para ver la instalación de primera mano y luego comencé a hablar con GEW. Al principio, lentamente, porque sabíamos que necesitábamos una solución compleja y de ingeniería con un alto nivel de personalización”. Poco a poco, el impulso fue cobrando fuerza a medida que trabajaba en los requisitos de Panoval con la división “Especialista UV” de GEW. Comenta: “Quedamos impresionados con la gente de GEW… su capacidad de respuesta y su capacidad para responder a todas nuestras preguntas, por técnicas que fueran. Se trata de trabajar con las personas adecuadas”.
Luego, Van Zwieten visitó las instalaciones de producción de GEW en el Reino Unido durante la construcción del sistema, lo que brindó a ambas partes la oportunidad de discutir el sistema con más detalle y asegurarse de que estaba en camino para cumplir con todos los requisitos y expectativas. En cuanto al diseño, la instalación y el soporte técnico continuo del sistema, van Zwieten no tiene reservas: “Todo el proceso fue perfecto, no hemos tenido ningún problema. Si surge un problema técnico, contamos con el monitoreo remoto de GEW para ayudarnos, pero realmente hemos tenido una buena experiencia con este sistema. Y continúa: “Hasta la fecha, la única demanda que hemos tenido para el servicio de monitoreo remoto son los informes semanales que recibimos automáticamente, que nos muestran información de gestión útil, como el tiempo de funcionamiento, las horas de lámpara, el uso de energía y la eficiencia. También nos da tranquilidad porque sabemos que si surgiera un problema, la plataforma de monitoreo lo detectaría inmediatamente”.
Como señala van Zwieten, no se escatimaron gastos en la especificación del nuevo sistema de curado UV, para garantizar que satisfaga todas las demandas en los años venideros. Comenta: “Un laminador típico instalará una o dos estaciones de lámparas y estará satisfecho. Nos hemos diferenciado aquí e instalamos una serie de cinco lámparas en tándem, lo que significa que podemos modificar la distancia entre la aplicación química y el curado de un trabajo a otro, lo que nos permite atender a muchos mercados diferentes que actualmente no pueden atenderse con esta tecnología. . Por eso elegimos trabajar junto con la gente de GEW, ellos tienen los conocimientos técnicos y la experiencia para un sistema tan complejo. Ahora esperamos un rápido retorno de nuestra inversión, con el ahorro de energía y el nuevo trabajo que el sistema UV nos está aportando”.
Los mercados objetivo de Panoval son las industrias farmacéutica y electrónica, que requieren una etiqueta más limpia con menores propiedades de desgasificación residual. Van Zwieten explica: “La desgasificación residual es cuando un producto continúa emitiendo gases después de su producción, y esto puede ser un problema grave para los fabricantes. En el mundo de la electrónica, por ejemplo, la desgasificación puede causar fallas electrónicas y si se fabrican artículos costosos como unidades ópticas, entonces cualquier factor de falla debe reducirse al mínimo absoluto, si no se puede erradicar por completo”. Y continúa: “Aquí es donde el sistema de curado UV realmente nos diferencia. Hemos probado nuestro proceso de curado en nuestro entorno de producción de sala limpia ISO 6 y podemos producir laminados con propiedades de desgasificación mucho, mucho más bajas. Esto nos permite ofrecer un producto más limpio y muy superior a estos fabricantes especializados y sus convertidores”.
Con el sistema UV diseñado específicamente para Panoval, la distancia entre los cabezales de recubrimiento y las lámparas de curado se puede controlar con precisión. Esto significa que se puede lograr la exposición óptima para una multitud de aplicaciones diferentes. Además, el sistema UV ha sido diseñado con siete carcasas de faros y cinco casetes de lámpara reposicionables, lo que significa que los faros se pueden colocar en varias posiciones diferentes para controlar eficazmente el tiempo de permanencia. Al aumentar el tiempo entre la aplicación de productos químicos al sustrato y el punto en el que se curan esos productos químicos, se permite más tiempo para que escapen los gases no deseados antes de la laminación. También afecta la velocidad a la que puede funcionar la máquina; el período de desgasificación más largo permite lograr un curado efectivo y seguro a velocidades de funcionamiento hasta un 50 % más rápidas. Como dice van Zwieten: “Esto nos da una enorme ventaja competitiva sobre muchas empresas estadounidenses y europeas, que se limitan a funcionar a velocidades más lentas”.
Para demostrar la búsqueda de la solución perfecta por parte de la empresa, Panoval también ha invertido en tener cinco sensores de monitoreo UV multipunto (mUVm) GEW instalados en cada uno de los cabezales de las lámparas UV y conectados a su sistema ERP. Estos pueden medirse en la posición central de la lámpara y en los bordes extremos de una red de 500 mm y una red de 1050 mm. Además de las lecturas del medidor de partículas que miden con precisión los niveles de desgasificación inmediatamente después del curado, mUVm permite al equipo de producción medir y verificar que se haya administrado el nivel correcto de dosis e intensidad de UV durante todo el ciclo de producción. Con mUVm es posible generar un certificado de curado UV para cada lote registrando las salidas de UV en vivo para cada lámpara. Los datos de salida UV en tiempo real se exportan a través de una interfaz API RESTful.
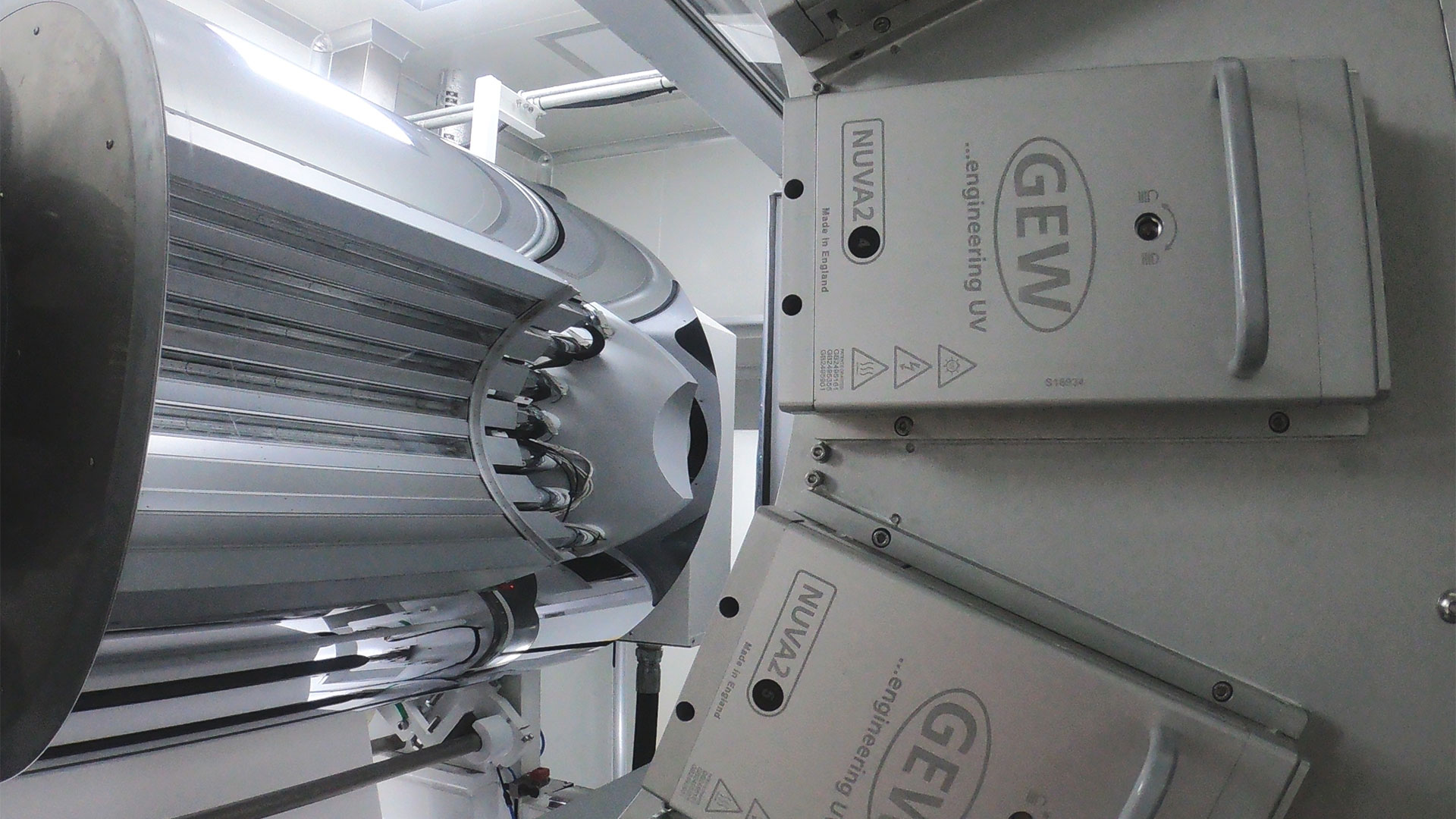
Sin embargo, el objetivo de van Zwieten es desarrollar aún más los beneficios del sistema de monitoreo UV mediante el uso de su capacidad de generación de informes para investigar y establecer niveles de energía óptimos para la adherencia, adherencia y liberación inicial de la gama principal de productos de la empresa. Esta información del sensor UV se utilizará luego para crear un mapa de curado en 3D de cada rollo gigante de producto, ofreciendo un alto nivel de trazabilidad a los fabricantes de usuarios finales. Si bien estos datos son particularmente cruciales para los clientes de las industrias farmacéutica, electrónica y aeroespacial, también se pueden utilizar para configurar series de producción repetidas, de manera rápida y eficiente.
El equipo de Wilco van Zwieten también tuvo que superar dificultades técnicas creadas por las condiciones locales en la ciudad de Ho Chi Minh. Los 18.000 m3/h de aire utilizados para la refrigeración ingresan a la sala blanca desde el exterior del edificio a una temperatura ambiente de aproximadamente 35 °C. Han instalado una filtración de dos etapas y unos 25 metros de conductos de entrada adicionales para reducir la temperatura del aire, la humedad y cualquier partícula contaminante en su interior, antes de que llegue a los cabezales de las lámparas.
El equipo de producción está impulsado colectivamente por una mentalidad pionera; su objetivo es utilizar la investigación y el desarrollo para crear productos que ofrezcan al usuario final una ventaja comercial. Un ejemplo de esto es su producción de sustrato para etiquetas de neumáticos, utilizando un refinado proceso de fusión en caliente UV. Como explica van Zwieten: “No utilizaríamos el termofusible convencional para las etiquetas de neumáticos, ya que es bastante inestable, especialmente en gramajes más altos. Esto da como resultado que el convertidor tenga que reducir la velocidad de conversión ya que las cuchillas de troquelado se contaminan rápidamente con adhesivo. En cambio, hemos perfeccionado el proceso de termofusión UV mediante el cual podemos sobrecurar ligeramente para crear un adhesivo de baja pegajosidad que tiene una adhesión final muy alta. Esto significa que el convertidor puede producir sus etiquetas mucho más rápido y de forma más limpia. Es una situación en la que todos salimos ganando”.
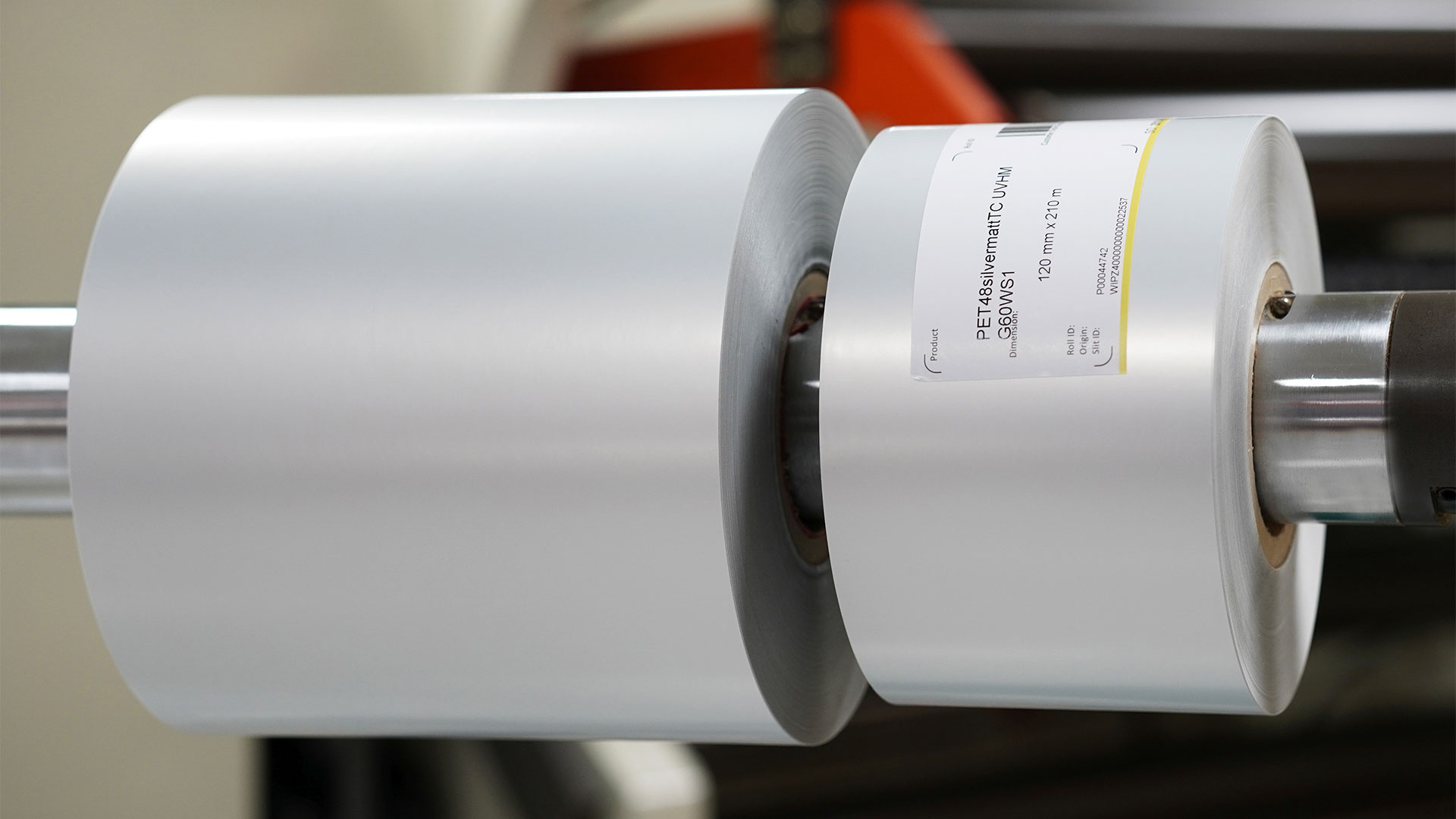
Son los beneficios comerciales posteriores los que diferencian sus productos UV de los convencionales y compensan con creces el costo algo mayor de las materias primas basadas en UV. Además, van Zwieten señala una tendencia del mercado que también juega a su favor: “Cada vez más fabricantes de barnices producen polímeros basados en UV y vemos que los precios caen rápidamente… ya han bajado más del 40% en el último año. últimos tres años. Es cuestión de tiempo hasta que los rayos UV tomen el relevo”.
El sistema de cinco lámparas de Panoval permite al equipo adaptar el proceso de curado a cada trabajo, para lograr un curado insuficiente o excesivo a voluntad. Como explica van Zwieten: “Para ciertos trabajos necesitamos un curado insuficiente y podemos hacerlo simplemente usando una lámpara al final del camino. La ventaja de esto es que extiende el recorrido hasta 130 cm, lo que permite que se produzca la desgasificación antes de que el recubrimiento llegue a la estación UV. De esta manera podemos producir etiquetas para aplicaciones médicas muy exigentes, por ejemplo, sin ralentizar nuestra línea de recubrimiento”.
Para cuantificar este aumento de velocidad en términos de ventaja competitiva, van Zwieten continúa: “Podemos realizar estos trabajos particulares a hasta 40 metros por minuto, lo que está muy por encima de la norma para este tipo de producto especializado. Normalmente funcionan en Europa y EE. UU. a 25 metros por minuto y, como resultado, son significativamente más caros en productos similares”.
El etiquetado para aplicaciones médicas suele ser necesario sobre sustratos no tejidos, que absorben mucha más radiación que los poliésteres y polipropilenos. Esto significa que un alto poder de curado UV también es un requisito habitual, y el sobrecurado se logra fácilmente con hasta 108 kW de potencia UV disponible. El sobrecurado UV se utiliza para imitar las propiedades más deseables de los adhesivos a base de solventes, mediante los cuales el recubrimiento se cura para volverse de baja pegajosidad y seco al tacto, pero al mismo tiempo sigue siendo un adhesivo altamente cohesivo que envejece extremadamente bien. Este proceso tiene otras ventajas, como explica van Zwieten: “La adherencia inicial es baja e incluso permite el reposicionamiento, pero la adhesión final es muy fuerte (supera fácilmente los 50 newtons) como se requiere para el etiquetado de alto rendimiento. Y luego volvemos a las ventajas de la conversión, que se convierte en un proceso mucho más rápido con recubrimientos curados con UV”. Y concluye: “Podemos lograr todos los beneficios de los recubrimientos a base de solventes, pero sin la desgasificación y los extraíbles, que tanto preocupan a las industrias médica, aeroespacial y electrónica”.
Panoval también tiene ventanas de cuarzo GEW ‘HiC’ instaladas en los cabezales de las lámparas UV, que son particularmente adecuadas para aplicaciones de fusión en caliente. Este grado especial de cuarzo permite que pase mucha más energía UVC al recubrimiento, en comparación con el cuarzo convencional. Como comenta van Zwieten: “No escatimamos esfuerzos en las especificaciones de nuestro sistema UV y todavía tenemos que encontrar un trabajo que no pueda realizar. Debido a que realizamos una gama amplia y diversa de trabajos exigentes y de corto plazo, teníamos que estar seguros de que siempre podremos lograr lo que queremos hacer. Y si alguna vez descubrimos que necesitamos más energía, podemos agregar fácilmente dos casetes de cabezales de lámpara más en las carcasas vacías”. Y añade: “Sin embargo, tal como están las cosas, en esta línea podemos circular a 220 metros por minuto. Estamos logrando el doble de velocidad de producción que una aplicación equivalente a base de solvente. Como ejemplo, recientemente produjimos una etiqueta de poliéster removible con un revestimiento de baja liberación de silicona a 100 metros por minuto con una cobertura de capa baja y cero desgasificación… y eso, hasta donde yo sé, es un nuevo récord mundial”.
“El sistema GEW ha logrado exactamente lo que queríamos. Se sobrecura, se cura perfectamente. Estamos ahorrando enormes cantidades en términos de consumo eléctrico y reduciendo nuestra huella de carbono. Si imaginas que nuestro antiguo sistema a base de agua requería casi 40 metros de hornos calentados a 200 grados para poder sacar el agua… estábamos consumiendo alrededor de 1.800kW por hora. Con los recubrimientos a base de agua, alrededor del 40% de cada kilo es agua que hay que extraer. Ahora con UV podemos correr a 220 metros por minuto y el máximo que consumimos ronda los 600kW por hora. Entonces es un tercio”.
Sin embargo, hay otras consideraciones que se deben tener en cuenta al adoptar procesos de curado UV, como señala van Zwieten: “Se necesita personal mejor capacitado y dedicado para trabajar con los rayos UV y comprenderlos, y, para empezar, se necesitan mejores equipos. En comparación, hay más de 1.100 laminadoras a base de solventes sólo en China, y son máquinas básicas, de bajo costo y fáciles de operar. No necesitas un laboratorio. Pero es un juego peligroso: es tóxico y contaminante, y cuesta mucha energía”. Comparando esto con los beneficios de los rayos UV, concluye: “Con los rayos UV no se necesita un incinerador, no es tóxico, no hay riesgo de incendio y el ahorro de energía y los beneficios ambientales son muy impresionantes”. Y concluye: “Hemos encontrado en GEW un socio muy competente y receptivo. A cualquiera que busque una solución UV para adhesivo termofusible, le sugeriría que los llame”.
Haga clic aquí para obtener más información sobre nuestro proceso UV especializado.